
October 5, 2024
Using coolants and lubricants with annular cutters offers several advantages that significantly enhance both performance and tool longevity. Annular cutters, used in magnetic core drilling machines, operate at high speeds and generate a lot of heat due to friction with the metal. Coolants and lubricants help in managing these conditions effectively.
#Annular Cutters #coolant #core drills #lubricant #mag drills #magdrill #magnetic core drilling machine #magnetic drilling machine #magnetic drilll press #magnetic drills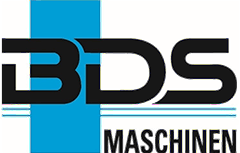

Advantages of Using Coolants & Lubricants for Annular Cutters
October 5, 2024
Using coolants and lubricants with annular cutters offers several advantages that significantly enhance both performance and tool longevity. Annular cutters, used in magnetic core drilling machines, operate at high speeds and generate a lot of heat due to friction with the metal. Coolants and lubricants help in managing these conditions effectively.
Key Advantages of Using Coolants & Lubricants for Annular Cutters:
- Improved Tool Life
- Heat Dissipation: Coolants absorb and dissipate heat generated during cutting, preventing excessive heat build-up that can damage or soften the cutting edge of the annular cutter.
- Reduced Wear and Tear: Proper lubrication minimizes friction between the cutting edges and the material being drilled, reducing the wear on the tool and prolonging its lifespan.
- Enhanced Cutting Performance
- Faster Cutting: Lubricants help reduce friction between the cutter and the metal surface, allowing the cutter to move more smoothly through the material, leading to faster drilling times.
- Smoother Operation: Lubrication allows for smoother chip evacuation and prevents metal chips from sticking to the cutter, resulting in more efficient cutting and less machine downtime.
- Prevention of Tool Breakage
- Stress Reduction: By reducing friction and heat, lubricants prevent the cutter from experiencing excessive stress, which can otherwise lead to cracking or breakage of the tool.
- Consistent Cooling: Coolants ensure the cutter stays within a manageable temperature range, avoiding thermal expansion or structural weakening that can lead to premature failure.
- Better Hole Quality
- Cleaner Cuts: Coolants and lubricants ensure that the annular cutter cuts through the metal cleanly without causing burrs or rough edges, resulting in smooth and precise holes.
- Reduced Material Hardening: High temperatures can cause localized hardening of the metal surface, making it more difficult to drill. Coolants help to maintain the metal’s original properties during the drilling process.
- Reduced Downtime
- Longer Tool Use Between Replacements: By prolonging tool life and reducing the frequency of tool wear, the use of coolants and lubricants helps minimize the need for frequent tool changes, thus reducing downtime during drilling operations.
- Efficient Chip Removal: Coolants help to flush out metal chips generated during cutting, ensuring smoother and uninterrupted operation of the tool.
- Energy Savings
- Lower Cutting Resistance: Lubricants decrease friction between the tool and the material, reducing the amount of energy required to complete the cut, thus saving on machine power consumption.
- Optimized Feed Rates: With lubricated cutters, it’s possible to run the machine at optimal speeds and feed rates without risking tool damage or excessive energy consumption.
- Improved Operator Safety
- Temperature Control: Excessive heat from drilling can cause burns or make the environment unsafe for the operator. Coolants help keep the cutting area cool, contributing to a safer working environment.
- Reduced Chip Adhesion: Lubricants prevent metal chips from sticking to the cutter, which can cause the machine to jam or malfunction, reducing the risk of accidents.
Types of Coolants & Lubricants Used for Annular Cutters:
- Liquid Coolants: Often water-soluble oils or emulsions that are sprayed or applied during drilling to cool and lubricate the cutter.
- Cutting Oils: These oils provide superior lubrication, especially for tougher materials. They may be applied directly to the cutting area or mixed with coolants.
- Paste Lubricants: Thicker paste lubricants are used for slower cutting operations or when working with vertical or overhead drilling, where liquid coolants may be difficult to apply.
- Mist Coolants: These are a mix of air and coolant sprayed as a mist to simultaneously cool and lubricate.
Conclusion:
Using coolants and lubricants with annular cutters leads to improved tool longevity, faster cutting, better hole quality, and increased operator safety. It ensures more efficient performance, less downtime, and a smoother operation, making it essential for maximizing the productivity and cost-effectiveness of metal drilling tasks.
#Annular Cutters #coolant #core drills #lubricant #mag drills #magdrill #magnetic core drilling machine #magnetic drilling machine #magnetic drilll press #magnetic drills
September 1, 2023
Twist drills and annular cutters are both tools used for drilling holes in various materials, but they have distinct differences in terms of design, application, efficiency, and performance. Let’s compare them in different aspects:
#Annular Cutters #compare twist drill with annular cutter #compare twist drill with broach core cutter #compare twist drill with core drills #core drills #drilling #Magnetic Drill Press #Magnetic Drilling Machines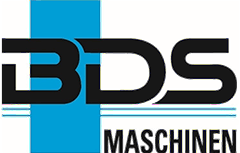

Comparing Twist Drills with Annular Cutters
September 1, 2023
Twist drills and annular cutters are both tools used for drilling holes in various materials, but they have distinct differences in terms of design, application, efficiency, and performance. Let’s compare them in different aspects:
Design:
Twist Drill: A twist drill is a common and simple design consisting of a pointed tip, spiral flutes, and a cylindrical shank. The flutes are responsible for removing material from the hole as the drill rotates.
Annular Cutter: An annular cutter or broach core cutter, has a more specialized design. It’s a hollow cylindrical tool with cutting teeth on the circumference and a center pilot pin. As the cutter rotates, it removes a solid slug or core of material, leaving a clean, smooth hole.
Application:
Twist Drill: Twist drills are versatile and suitable for drilling smaller holes in a wide range of materials, including metal, wood, plastic, and more. They are commonly used in DIY projects, general maintenance, and light manufacturing.
Annular Cutter: Annular cutters are primarily designed for drilling larger and deeper holes, especially in metal. They excel at creating holes in thick steel, stainless steel, and other tough materials. They are commonly used in fabrication, construction, and metalworking industries.
Hole Quality:
Twist Drill: While twist drills are efficient for small holes, they can produce rougher holes with burrs and irregularities, especially in harder materials.
Annular Cutter: Annular cutters produce higher-quality holes with smooth finishes and minimal burring. This is because they remove material from the circumference rather than forcing it out through flutes.
Efficiency:
Twist Drill: Twist drills are efficient for smaller holes, but they may require more force and time when drilling larger holes due to their design.
Annular Cutter: Annular cutters are more efficient for larger holes, as they remove material quickly and generate less heat due to their cutting method. This can lead to faster drilling times and increased tool life.
Precision:
Twist Drill: Twist drills can be accurate for general applications, but they might wander slightly when starting the hole, leading to less precise positioning.
Annular Cutter: Annular cutters offer better precision due to their center pilot pin, which helps guide the cutter accurately into the material, reducing the chances of wandering.
Tool Longevity:
Twist Drill: Twist drills can wear out relatively quickly when drilling tough materials or at high speeds due to friction and heat buildup.
Annular Cutter: Annular cutters are built to withstand the demands of drilling through tough materials, resulting in longer tool life and fewer instances of premature wear.
In summary, the choice between a twist drill and an annular cutter depends on the specific application and the size and material of the hole you need to create. Twist drills are more versatile for general use, while annular cutters excel in producing precise, clean, and efficient holes in larger dimensions, especially in tough materials like metal.
Annular Cutters: https://www.bds-machines.com/annular-cutters/
Twist Drills: https://www.bds-machines.com/accessories/machine-taps-with-weldon-shank/
#Annular Cutters #compare twist drill with annular cutter #compare twist drill with broach core cutter #compare twist drill with core drills #core drills #drilling #Magnetic Drill Press #Magnetic Drilling MachinesAugust 29, 2023
Each type has its own advantages and disadvantages, and the choice between them depends on the specific application, material being cut, and desired outcomes.
#Annular Cutters #broach core cutters #broach cutter #core drills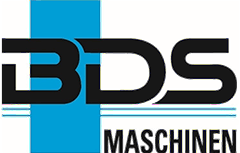

Comparison between TCT and HSS Annular Cutters
August 29, 2023
Tungsten Carbide Tipped (TCT) annular cutters and High-Speed Steel (HSS) annular cutters are two different types of cutting tools used for drilling holes in metal and other materials. Each type has its own advantages and disadvantages, and the choice between them depends on the specific application, material being cut, and desired outcomes. Here’s a comparison between TCT annular cutters and HSS annular cutters:
Tungsten Carbide Tipped (TCT) Annular Cutters:
- Durability and Longevity: TCT annular cutters feature a high-strength tungsten carbide cutting edge that provides exceptional durability and resistance to wear. This makes them well-suited for demanding applications and extended use without frequent replacements.
- Hard Material Compatibility: TCT cutters aka TCT broach core cutters excel at cutting through hard and abrasive materials such as stainless steel, hardened steel, cast iron, and non-ferrous metals. Their carbide cutting edges are capable of maintaining sharpness and edge integrity when subjected to tough materials.
- Higher Cutting Speeds: Due to their superior hardness and heat resistance, TCT annular cutters can handle higher cutting speeds compared to HSS cutters. This results in faster material removal and reduced machining time.
- Reduced Heat Generation: TCT cutters generate less heat during the cutting process, thanks to the carbide cutting edge’s ability to handle high temperatures. This can help minimize the risk of workpiece deformation and improve surface finish.
- Precision and Accuracy: TCT cutters maintain their sharpness for a longer time, contributing to consistent precision and accuracy in hole drilling. This is important when tight tolerances and precise dimensions are required.
- Limited Chip Evacuation: The design of TCT annular cutters may sometimes result in less efficient chip evacuation compared to some HSS cutters. Proper tool and machine setup are crucial to ensure smooth chip removal.
Product page of TCT annular cutters: https://www.bds-machines.com/types-of-annular-cutters/carbide-series-annular-cutters/
High-Speed Steel (HSS) Annular Cutters:
- Cost-Effectiveness: HSS annular cutters are generally more affordable than TCT cutters, making them a practical choice for applications that do not involve cutting through extremely hard materials.
- Versatility: While not as effective as TCT cutters with extremely hard materials, HSS annular cutters aka HSS broach core cutters are still versatile and suitable for a wide range of materials, including softer metals and mild steel.
- Easier Chip Evacuation: Many HSS annular cutters are designed with features to facilitate efficient chip evacuation, reducing the risk of chip buildup and ensuring smoother cutting.
- Lower Impact on Magnetic Drills: HSS cutters exert less stress on magnetic drilling machines, making them a preferred choice when working with lightweight or portable machines.
- Replacement and Sharpening: HSS cutters are easier to replace and can be sharpened more readily than TCT cutters. This can lead to reduced downtime and maintenance costs.
Product page of HSS annular cutters: https://www.bds-machines.com/types-of-annular-cutters/serie-hss-standard/
In summary, TCT annular cutters are the preferred choice for drilling through hard materials and demanding applications where durability, longevity, and high cutting speeds are crucial. HSS annular cutters are a more cost-effective option for general-purpose drilling in a variety of materials and can be suitable for applications where precision and high cutting speeds are not the primary concern. The choice between TCT and HSS annular cutters should be based on the specific requirements of the job at hand.
#Annular Cutters #broach core cutters #broach cutter #core drills