
October 5, 2024
Using coolants and lubricants with annular cutters offers several advantages that significantly enhance both performance and tool longevity. Annular cutters, used in magnetic core drilling machines, operate at high speeds and generate a lot of heat due to friction with the metal. Coolants and lubricants help in managing these conditions effectively.
#Annular Cutters #coolant #core drills #lubricant #mag drills #magdrill #magnetic core drilling machine #magnetic drilling machine #magnetic drilll press #magnetic drills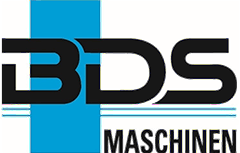

Advantages of Using Coolants & Lubricants for Annular Cutters
October 5, 2024
Using coolants and lubricants with annular cutters offers several advantages that significantly enhance both performance and tool longevity. Annular cutters, used in magnetic core drilling machines, operate at high speeds and generate a lot of heat due to friction with the metal. Coolants and lubricants help in managing these conditions effectively.
Key Advantages of Using Coolants & Lubricants for Annular Cutters:
- Improved Tool Life
- Heat Dissipation: Coolants absorb and dissipate heat generated during cutting, preventing excessive heat build-up that can damage or soften the cutting edge of the annular cutter.
- Reduced Wear and Tear: Proper lubrication minimizes friction between the cutting edges and the material being drilled, reducing the wear on the tool and prolonging its lifespan.
- Enhanced Cutting Performance
- Faster Cutting: Lubricants help reduce friction between the cutter and the metal surface, allowing the cutter to move more smoothly through the material, leading to faster drilling times.
- Smoother Operation: Lubrication allows for smoother chip evacuation and prevents metal chips from sticking to the cutter, resulting in more efficient cutting and less machine downtime.
- Prevention of Tool Breakage
- Stress Reduction: By reducing friction and heat, lubricants prevent the cutter from experiencing excessive stress, which can otherwise lead to cracking or breakage of the tool.
- Consistent Cooling: Coolants ensure the cutter stays within a manageable temperature range, avoiding thermal expansion or structural weakening that can lead to premature failure.
- Better Hole Quality
- Cleaner Cuts: Coolants and lubricants ensure that the annular cutter cuts through the metal cleanly without causing burrs or rough edges, resulting in smooth and precise holes.
- Reduced Material Hardening: High temperatures can cause localized hardening of the metal surface, making it more difficult to drill. Coolants help to maintain the metal’s original properties during the drilling process.
- Reduced Downtime
- Longer Tool Use Between Replacements: By prolonging tool life and reducing the frequency of tool wear, the use of coolants and lubricants helps minimize the need for frequent tool changes, thus reducing downtime during drilling operations.
- Efficient Chip Removal: Coolants help to flush out metal chips generated during cutting, ensuring smoother and uninterrupted operation of the tool.
- Energy Savings
- Lower Cutting Resistance: Lubricants decrease friction between the tool and the material, reducing the amount of energy required to complete the cut, thus saving on machine power consumption.
- Optimized Feed Rates: With lubricated cutters, it’s possible to run the machine at optimal speeds and feed rates without risking tool damage or excessive energy consumption.
- Improved Operator Safety
- Temperature Control: Excessive heat from drilling can cause burns or make the environment unsafe for the operator. Coolants help keep the cutting area cool, contributing to a safer working environment.
- Reduced Chip Adhesion: Lubricants prevent metal chips from sticking to the cutter, which can cause the machine to jam or malfunction, reducing the risk of accidents.
Types of Coolants & Lubricants Used for Annular Cutters:
- Liquid Coolants: Often water-soluble oils or emulsions that are sprayed or applied during drilling to cool and lubricate the cutter.
- Cutting Oils: These oils provide superior lubrication, especially for tougher materials. They may be applied directly to the cutting area or mixed with coolants.
- Paste Lubricants: Thicker paste lubricants are used for slower cutting operations or when working with vertical or overhead drilling, where liquid coolants may be difficult to apply.
- Mist Coolants: These are a mix of air and coolant sprayed as a mist to simultaneously cool and lubricate.
Conclusion:
Using coolants and lubricants with annular cutters leads to improved tool longevity, faster cutting, better hole quality, and increased operator safety. It ensures more efficient performance, less downtime, and a smoother operation, making it essential for maximizing the productivity and cost-effectiveness of metal drilling tasks.
#Annular Cutters #coolant #core drills #lubricant #mag drills #magdrill #magnetic core drilling machine #magnetic drilling machine #magnetic drilll press #magnetic drills
September 19, 2024
Cleaning a Morse taper spindle is crucial for maintaining the precision and performance of your machine tool. Here’s a step-by-step guide:
#mag drills #magdrill #magnetic core drilling machine #magnetic drilling machine #magnetic drilll press #magnetic drills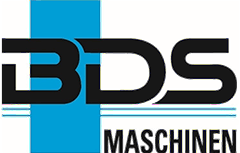

How to clean a Morse Taper Spindle?
September 19, 2024
Cleaning a Morse taper spindle is crucial for maintaining the precision and performance of your machine tool. Here’s a step-by-step guide:
Tools and Materials You’ll Need:
- Lint-free cloth or cleaning rags
- Solvent or degreaser (e.g., isopropyl alcohol or a machine-specific cleaner)
- Soft nylon brush
- Compressed air (optional)
- Taper cleaner or reamer (optional, for more thorough cleaning)
Steps:
1. Power Off and Secure the Machine:
Ensure the machine is powered off and properly secured to prevent any accidental movement.
2. Remove the Tooling:
Carefully remove any tooling or accessories attached to the spindle.3
3. Initial Wipe Down:
Use a lint-free cloth to wipe down the spindle to remove loose debris, oil, or grime.
4. Apply Solvent/Degreaser:
Moisten a clean cloth with the solvent or degreaser and wipe the inside of the taper. Avoid soaking the spindle with too much liquid.
If necessary, use a soft nylon brush to gently scrub the inside of the spindle taper. This helps remove any stubborn residue.
5. Use Compressed Air:
If available, use compressed air to blow out any remaining debris or liquid. Hold the air nozzle at an angle to avoid blowing debris deeper into the spindle.
Ensure the spindle is dry before proceeding to the next step.
6. Inspect the Taper:
Visually inspect the inside of the taper for any remaining dirt, debris, or damage. The surface should be clean and smooth.
7. Optional: Use a Taper Cleaner/Reamer:
For a more thorough cleaning, you can use a Morse taper cleaner or reamer. This tool is designed to fit the taper and remove any small debris or imperfections without damaging the spindle.
Insert the taper cleaner into the spindle and rotate it as recommended by the tool’s manufacturer.
8. Final Wipe Down:
Use a clean, dry cloth to give the taper a final wipe-down, ensuring it’s completely clean and dry.
9. Reinstall Tooling:
Once the spindle is clean, reinstall the tooling carefully, making sure it seats properly within the taper.
Tips:
- Regular Maintenance: Regular cleaning after each use will help maintain the spindle’s accuracy and longevity.
- Avoid Contamination: Always use clean tools and materials to prevent introducing new contaminants into the spindle.
- Check for Wear: While cleaning, take the opportunity to check for any wear or damage that might affect the spindle’s performance.
This process should keep your Morse taper spindle in good working order, ensuring optimal machine performance.
#mag drills #magdrill #magnetic core drilling machine #magnetic drilling machine #magnetic drilll press #magnetic drillsSeptember 9, 2023
Magnetic drilling machines offer a combination of precision, safety, efficiency, and versatility that make them indispensable tools in industries that require accurate hole drilling in metal materials. Their ability to work in various orientations and their portability further enhance their value in a wide range of applications.
#mag drills #magdrill #magnetic core drilling machine #magnetic drilling machine #magnetic drilll press #magnetic drills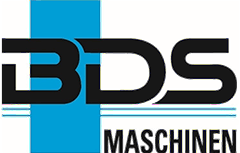

Advantages of Magnetic Drilling Machines
September 9, 2023
Magnetic drilling machines, also known as mag drills or magnetic drill presses, offer several advantages in various industries and applications. Here are some of the key advantages of using magnetic drilling machines:
Portability:
Many magnetic drilling machines are designed to be relatively lightweight and portable, making them suitable for on-site work or in locations where a fixed drill press is not practical. This portability enhances their usability in remote or confined spaces.
Versatility:
Magnetic drilling machines are highly versatile and can be used in a wide range of applications, including metal fabrication, construction, shipbuilding, and more. They can drill holes in horizontal, vertical, and overhead positions, making them suitable for various orientations and angles.
Precision and Accuracy:
These machines offer high precision and accuracy when drilling holes. The magnetic base ensures stability and minimizes vibrations, resulting in clean and accurately positioned holes. This is crucial in industries where precise hole placement is essential.
Time Efficiency:
Magnetic drilling machines are designed to be fast and efficient. The magnetic base allows for quick setup and repositioning, reducing downtime. The powerful motor and specialized cutting tools also enable fast drilling, contributing to increased productivity.
Safety:
Traditional drilling methods often involve clamping materials, which can sometimes be unsafe or result in damage to the workpiece. Magnetic drilling machines eliminate the need for clamping, as the magnetic base securely holds the machine in place. This enhances operator safety and reduces the risk of workpiece distortion.
Large Hole Diameter Capability:
Magnetic drilling machines are capable of drilling large-diameter holes in metal surfaces, which can be challenging or impossible with conventional drilling methods. This is particularly useful in industries that require large holes for specific applications.
Reduced Material Damage:
Since magnetic drilling machines don’t require clamping, there’s minimal risk of damaging the workpiece due to excessive pressure or distortion. This is important when working with sensitive or expensive materials.
Ease of Use:
Magnetic drilling machines are designed with user-friendliness in mind. They often feature intuitive controls and ergonomic designs, making them accessible to both experienced operators and those new to using such equipment.
Cost Savings:
While the initial investment in a magnetic drilling machine might be higher compared to traditional drilling methods, the efficiency and precision they offer can lead to cost savings in the long run. Reduced labor time, increased productivity, and minimized material waste contribute to overall cost-effectiveness.
Adaptable to Various Materials:
Magnetic drilling machines are not limited to specific types of metals. They can work on a wide range of ferrous materials, including steel, stainless steel, and more.
#mag drills #magdrill #magnetic core drilling machine #magnetic drilling machine #magnetic drilll press #magnetic drillsIn summary, magnetic drilling machines offer a combination of precision, safety, efficiency, and versatility that make them indispensable tools in industries that require accurate hole drilling in metal materials. Their ability to work in various orientations and their portability further enhance their value in a wide range of applications.